Over the past five years, we’ve resisted the temptation to dramatically change Atom Amp(+) due to its strong reputation and reliability–no need to change what works well. However, we believe there is always room for improvement, and we’re excited to introduce Atom Amp 2 and Atom DAC 2. Atom Amp 2 is the best Atom […]
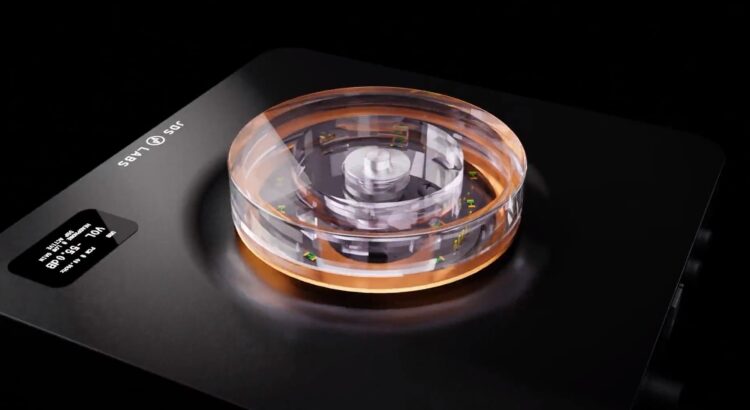
Element III MK2 = New Knob and EQ Firmware
Today we’re pleased to present Element III MK2! Before diving into what has changed, let’s clarify what MK2 means. This suffix distinguishes the “knob feel” of the original Element III from our latest hardware. The original Element III knob was designed for a loose and free spinning feel. Feedback from thousands of customers led us […]
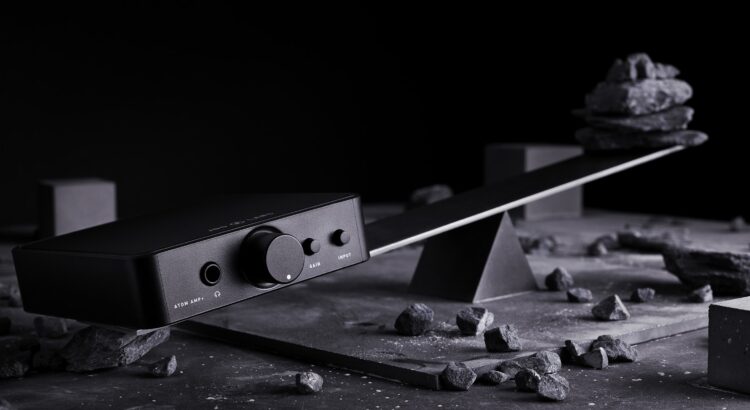
Introducing Atom Amp+ Hevi: Aluminum Knob, Rugged, Engravable
We’re pleased to present Atom Amp+ Hevi ! With around 40,000 Atom Amps and DACs shipped since 2018, we’ve been thrilled with its continued success. We’ve received more positive feedback than we ever could’ve expected, but we’ve also received some valid suggestions. That’s where the Atom Amp+ Hevi comes in. Many have asked for an […]
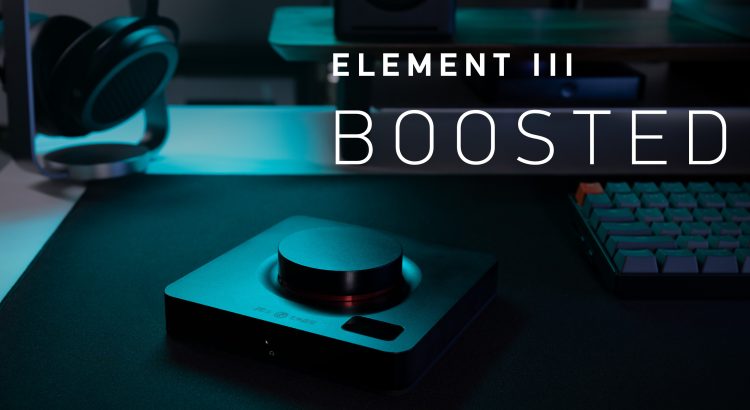
We Boosted Element III’s Output Power
We’ve long maintained that most headphones on the market need below 1W of power for normal listening. This is why all of our recent amplifiers have been designed around this figure–until now. Element III Boosted is for those of you with an appetite for ill-advised volumes from the world’s most power-hungry headphones. No, we still […]
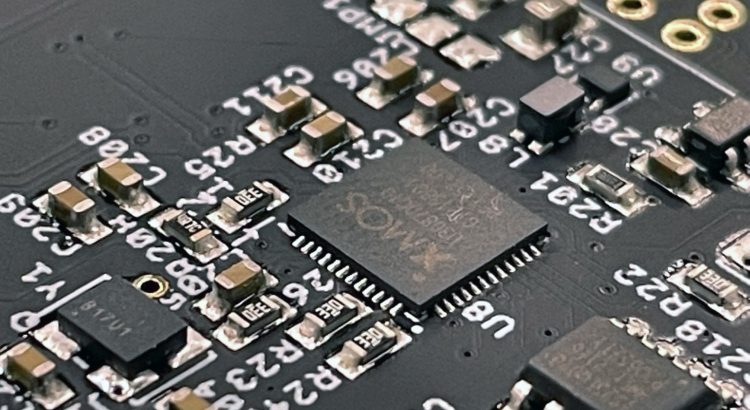
On EL3 Manufacturing
Element III manufacturing has been challenging, to say the least. We were ecstatic to release Element III and pleased to see a strong reception from customers all over the world. Thank you! Then a few things went frustratingly wrong. Like knobs which arrived wobbly or broken, or DACs which threw error codes upon arrival (yes, […]
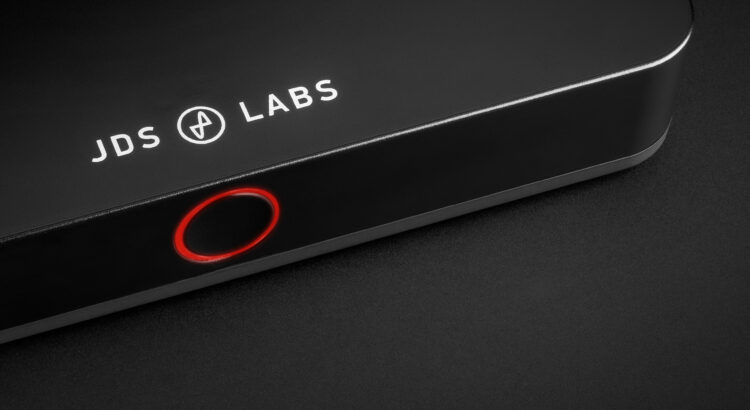
Introducing EL DAC II+ Balanced
EL DAC II+ Balanced pairs with EL Amp II+ Balanced, running on our latest XMOS based UAC2 engine with ASIO support for both PCM and DSD. Its balanced outputs are in addition to single-ended RCA outputs, giving you the flexibility to connect to any amplifier. Firmware EL DAC II+ Balanced arrives loaded with our latest […]
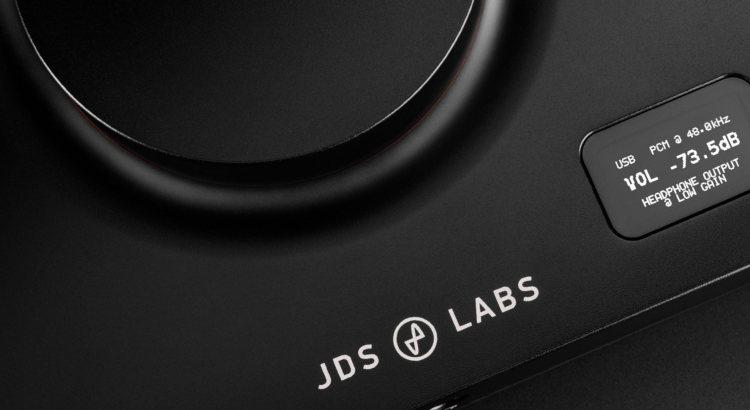
Element III Firmware Updates & Menu Options
Thank you to all first adopters of Element III! We’re glad so many of you are enjoying Element III as much as we are. While EL3 is temporarily sold out, we’ve been listening to all feedback to improve firmware features and overall quality (more coming in a separate post). Most notably, Firmware v2.2.0 or newer […]
Introducing EL Amp II+ Balanced
JDS Labs EL Amp II+ Balanced We’ve historically avoided building balanced amplifiers because well designed, single-ended amplifiers are all most need in a home audio setup. Yet, a growing number of customers have asked for balanced inputs. Maybe you have an audio interface or source with XLR or TRS outputs, and have passed on EL […]
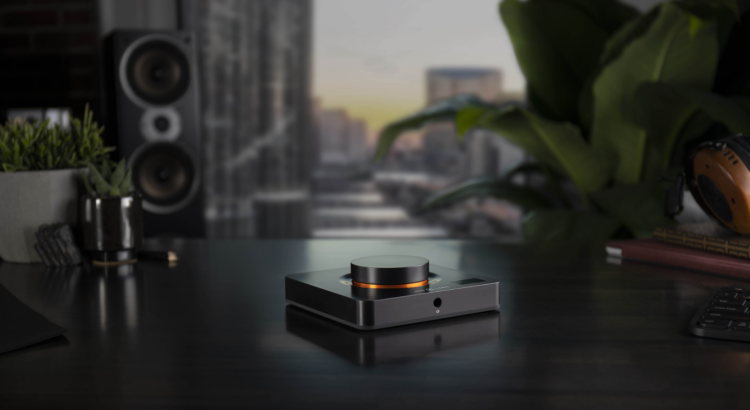
JDS Labs Element III – Official Release & Benchmarks
JDS Labs Element III We’re incredibly pleased to present Element III. This is no ordinary refresh. Rather, we’ve reimagined our flagship amp+DAC to create a listening experience you will actually notice and appreciate. Element III runs on our second generation XMOS hardware and firmware, blissfully integrated with a custom encoder. You’ll hear perfect channel balance […]
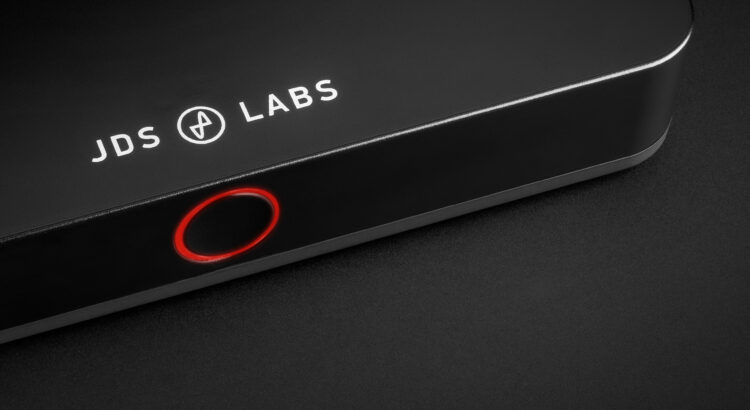
Introducing EL DAC II+: Element III or EL Stack?
JDS Labs EL DAC II+ EL DAC II+ transitions EL DAC II from an AKM to an ESS chipset, building upon the same core feature set: relay muting, an XMOS based UAC2 engine, TOSLINK input, and transformer isolated coaxial S/PDIF input. The upgraded ESS chipset achieves higher performance and adds DSD128 support, and for those […]